Supply chain downside adaptability refers to how efficiently a business can reduce its operations, production, or resource usage when demand or capacity suddenly drops. At Calcviva, we specialize in helping supply chain managers, analysts, and business leaders understand and measure this adaptability with clear formulas and data. In real-world operations, supply chains are often built for growth and expansion. However, the ability to scale down is just as important, especially in unpredictable economic conditions. Even if caused by demand fluctuation, raw material shortages, or logistical breakdowns, your supply chain must be ready to operate at reduced levels without increasing costs or reducing efficiency.
This concept is vital across industries, from manufacturing and retail to healthcare and agriculture. A well-structured supply chain must remain lean and cost-effective during downturns. At Calcviva, our platform provides calculation tools and benchmarking metrics that help businesses simulate downside adaptability using real-time inputs and predictive algorithms. Understanding this metric empowers organizations to respond intelligently, avoid overproduction, reduce holding costs, and maintain resilience. This article provides a full guide on how to calculate supply chain downside adaptability using structured steps, formulas, SCOR metrics, and performance benchmarks.
Table of Contents
What Is Supply Chain Downside Adaptability?
Supply chain downside adaptability is the capability of a supply chain to reduce its output, volume, or service level in response to a demand decrease or supply-side shock. It is a core resilience metric in supply chain management and is also recognized in global standards like the SCOR (Supply Chain Operations Reference) model. At Calcviva, we define downside adaptability as the maximum percentage by which supply chain activities can be safely scaled down within a given timeframe, without triggering losses in quality, customer service, or compliance.
This metric becomes particularly valuable in turbulent market conditions. Companies must avoid stockpiling excess inventory, overcommitting to supplier orders, or running production lines beyond market needs. A business with poor downside adaptability risks high storage costs, waste, and revenue loss. Adaptability does not mean halting operations altogether, it involves making intentional, data-based reductions while still meeting critical service goals. The formula used to assess this capability gives decision-makers a percentage-based view of how much they can flex operations downward.
Understanding this concept is the first step to managing risk, improving planning systems, and staying competitive under pressure.
Role in Risk Management
Downside adaptability is a strategic tool in risk management. In traditional models, most planning focuses on how to grow and scale. However, when disruptions occur, like a sudden drop in consumer demand, political instability, or factory shutdowns, organizations must quickly shift gears to avoid unnecessary costs. Calcviva.com supports businesses in evaluating how flexible their supply chain is in scaling down operations while maintaining performance standards.
Risk managers use downside adaptability to answer key questions:
- How much can we reduce production without affecting delivery timelines?
- Can our suppliers handle order reductions without penalties?
- What is the minimum inventory level needed to keep operations stable?
This metric also intersects with supply chain resilience, agility, and continuity planning. By quantifying adaptability, companies can prepare predefined action plans and trigger thresholds. For instance, if orders drop by 30%, a business can confidently reduce factory shifts, slow down procurement, or reroute logistics based on adaptable capacity.
Regulatory bodies and supply chain auditors are increasingly prioritizing such metrics to evaluate compliance with sustainable, lean, and responsive practices. At Calcviva, we integrate this measurement into decision support tools for real-time simulations and threshold alerts.
When and Why to Measure Supply Chain Downside Adaptability
Situations Requiring Measurement
Businesses need to measure downside adaptability proactively, not just during a crisis. It plays a critical role during planning, budgeting, and supplier negotiations. Common scenarios that demand this measurement include:
- Demand crashes due to economic downturns, seasonal shifts, or competitor disruption
- Supplier interruptions like shortages, bankruptcies, or logistic failures
- Factory issues such as machine breakdown, labor shortage, or utility failure
- Market exits where a product is discontinued or phased out
- Compliance restrictions, including environmental limits or regulatory cuts
In each case, without a clear understanding of how quickly and effectively operations can scale down, businesses risk running unprofitable units or violating service-level agreements. Calcviva’s adaptability module provides a planning buffer by using historical and predictive data to estimate how operations react under stress conditions.
The goal is not just survival, but smooth adjustment. Measuring adaptability before disruptions occur gives companies more options and better outcomes when changes happen.
Benefits of Supply Chain Downside Adaptability
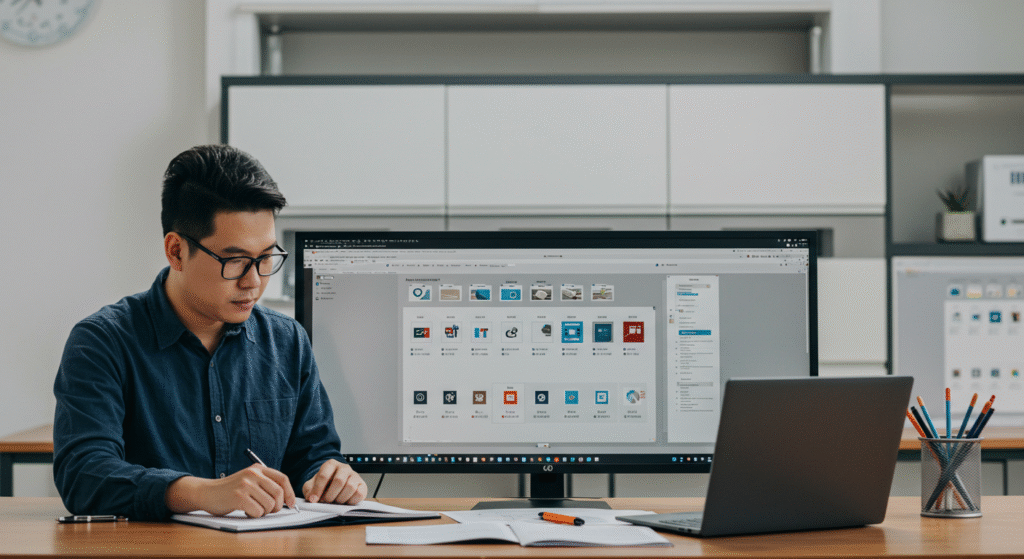
The benefits of tracking and optimizing supply chain downside adaptability are both operational and strategic. First, it directly reduces costs by minimizing overproduction, warehouse overflow, and excess labor. Second, it improves response speed, letting managers act early when signs of slowdown emerge. This metric also supports supplier flexibility, enabling smarter contracts that include reduction clauses or cancellation leeway.
Here’s a table summarizing key benefits:
Benefit | Impact |
Lower Inventory Costs | Avoids excess stock during demand drops |
Labor Efficiency | Reduces unneeded shifts or overtime costs |
Improved Planning Accuracy | Enables proactive adjustments |
Stronger Supplier Relationships | Builds trust with flexible order handling |
Higher Resilience | Sustains service with reduced inputs |
Additionally, tracking this metric supports better integration with SCOR-based performance measurement systems, allowing alignment with global supply chain best practices. At Calcviva, we’ve designed our system to help businesses monitor these benefits over time through dashboards and simulation tools.
Key Metrics to Track
Downside adaptability in the supply chain cannot be managed effectively without a clear set of measurable performance indicators. The most widely accepted framework for tracking adaptability is the SCOR (Supply Chain Operations Reference) model, developed by APICS (now part of ASCM). This model categorizes adaptability as part of overall supply chain responsiveness and agility.
One of the core SCOR metrics for this purpose is DSAD – Downside Supply Chain Adaptability. It measures the percentage reduction in output or throughput that a supply chain can accommodate within a specified time window, without significant cost penalties or service failure.
In addition to DSAD, other related SCOR adaptability metrics include:
- Upside Supply Chain Flexibility (USF) – The time required to increase production or fulfillment rate
- Upside Adaptability (USA) – The percentage increase possible in output
- Order Fulfillment Cycle Time (OFCT) – How quickly orders can be adjusted or fulfilled under change
- Perfect Order Fulfillment Rate (POFR) – Impacted indirectly by adaptability efficiency
Metric Name | Definition | Relevance to Downside Adaptability |
DSAD (Downside Adaptability) | % maximum output reduction within a defined period | Primary metric for adaptability measurement |
USF (Flexibility) | Time to adjust operations or output levels | Shows how quickly changes can be implemented |
OFCT | Time from order to delivery adjustment | Reflects lead-time under adaptability |
POFR | Rate of error-free, on-time deliveries | Decreases if adaptability is poorly managed |
At Calcviva.com, our tools are aligned with these SCOR metrics. We enable users to input real-world capacity, forecast scenarios, and lead times, generating live adaptability percentages based on actual data.
How to Calculate Downside Adaptability
The process of calculating downside adaptability involves analyzing how much output the supply chain can reduce, how fast it can achieve that reduction, and what systems or processes are affected. Below are the four key steps required for a complete measurement.
Step 1 – Set Baseline Output
Begin by establishing a reliable benchmark of your current or normal operating capacity. This includes:
- Daily or weekly production volume
- Order fulfillment rate
- Inventory turnover rate
- Supply procurement quantities
- Average lead times for inbound and outbound goods
This baseline represents your steady-state, the point from which reductions will be measured. It’s important to use data from a non-volatile period for accuracy. For example, if your plant produces 500 units per day under regular demand, that is your baseline.
Use historical data from ERP systems, warehouse reports, or your Calcviva dashboard to establish these figures. Document these clearly, as they form the reference point for percentage reduction in later steps.
Step 2 – Define Stress Scenario
Downside adaptability is not a theoretical metric. It is triggered by real-world disruption scenarios. These could include:
- A 30–50% demand drop due to economic decline
- A supplier lead time increase from 5 days to 14 days
- Container shortage or transportation bottlenecks
- Labor strikes, fuel price surges, or geopolitical issues
For accurate adaptability analysis, simulate these events or use recent historical disruptions. A demand drop scenario might look like this:
Scenario: Customer demand decreases from 500 units/day to 300 units/day over 2 weeks due to a global market slowdown.
At Calcviva, we help users define these scenarios dynamically, using probability ranges, cost tolerances, and supply chain mapping.
Step 3 – Measure Output Reduction Capability
Now that the baseline and stress scenario are defined, calculate how much of your operations can be safely scaled down without affecting quality, delivery, or profitability.
Use the following formula:
Downside Adaptability (%) = (Maximum Reduction in Output / Baseline Output) × 100
Example Calculation:
- Baseline production = 500 units/day
- Minimum safe output under stress = 320 units/day
- Maximum reduction = 180 units/day
Downside Adaptability = (180 / 500) × 100 = 36%
This means your supply chain can safely reduce its output by 36% in response to a defined stress event. The goal is to maximize this percentage while maintaining service continuity. This measurement provides insight into your supply chain’s scaling efficiency, responsiveness, and flexibility under pressure.
The Calcviva engine includes templates for this calculation and allows the inclusion of custom reduction triggers and tolerances.
Step 4 – Measure Time to Adapt
Time is a crucial variable in supply chain adaptability. It’s not just how much you can reduce but how quickly. For this, measure the lead time required to complete the reduction safely.
Key variables to track:
- Time to reduce production to target level
- Supplier response time to cancel or delay orders
- Inventory clearance or adjustment lag
- Workforce realignment time (shift cuts, schedule changes)
Let’s consider an example:
Reduction target: From 500 units/day to 320 units/day
Time taken to adjust: 12 days
This time-to-adjust value becomes your Downside Adaptation Lead Time, and it should be tracked consistently over different product lines, suppliers, or facilities. The shorter the adaptation time, the more agile and resilient your supply chain is.
Calcviva provides visual reports on adaptation lead time, allowing businesses to benchmark by product, region, or supplier. This helps in identifying bottlenecks and building contingency plans.
Tools and Data Required
Accurate calculation and improvement of supply chain downside adaptability require the integration of several data sources and tools. At Calcviva.com, we simplify this process by offering a centralized dashboard where users can input and analyze operational data across procurement, production, distribution, and inventory.
To effectively calculate adaptability, the following tools and data sets are required:
- ERP System Integration – For baseline data: production rates, lead times, order histories
- SCM Software – For supply planning, demand forecasting, and vendor schedules
- Scenario Modeling Tools – To simulate disruption events and demand fluctuations
- Real-time Monitoring Dashboards – For live tracking of fulfillment rate, cycle time, and inventory levels
- Supplier Communication Systems – To track vendor flexibility and cancellation lead times
- KPI Reporting Tools – To monitor adaptability percentage, time-to-adapt, and cost variance
Key data inputs include:
Data Type | Description |
Production Data | Output volume, shift capacity, downtime |
Demand Forecast | Predicted vs. actual sales |
Supplier Data | Response time, order flexibility |
Inventory Turnover | Buffer stock levels, reorder points |
Cost Structures | Variable vs. fixed cost during reduction |
Calcviva’s adaptability calculator combines these inputs to compute downside response capability, adaptation lead time, and cost avoidance metrics. All calculations align with SCOR definitions, ensuring compatibility with global benchmarks.
How to Improve Downside Adaptability
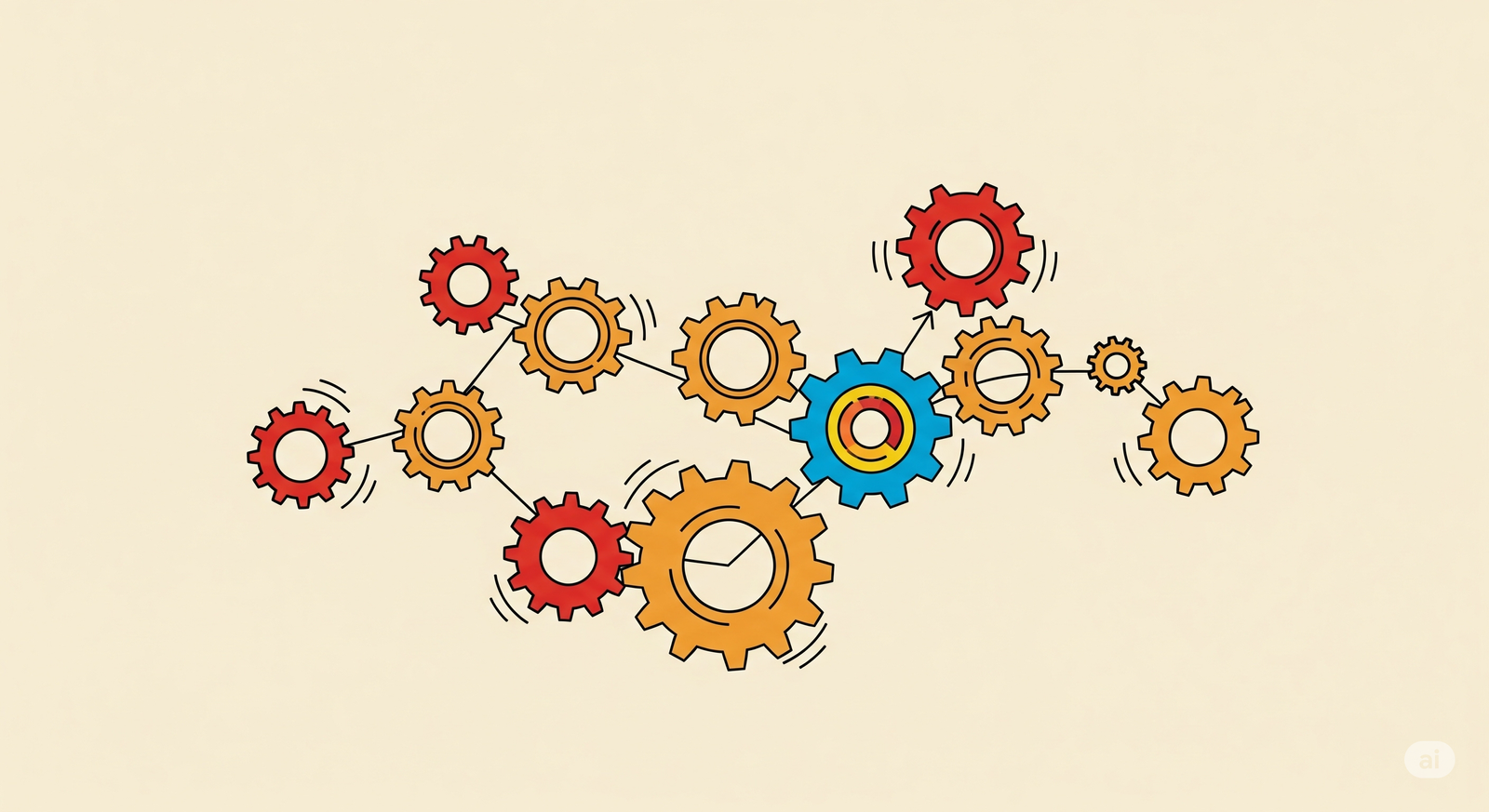
Once you’ve calculated your downside adaptability, the next step is to enhance it. High adaptability reduces cost, increases resilience, and improves customer service under disruption. Here are the top strategies for improving supply chain downside adaptability:
- Flexible Supplier Contracts
Renegotiate contracts to include clauses for reduction in volume without penalty. Use dual sourcing or tiered vendors to enable agility. - Modular Production Design
Structure production processes so they can be scaled down in sections rather than shut down entirely. Introduce parallel workflows with independent capacity. - Cross-Training Staff
Build labor flexibility by training workers across tasks. This allows you to reduce headcount temporarily without losing process knowledge. - Buffer Inventory Management
Use dynamic inventory policies that reduce buffer stock during slowdowns. Combine ABC classification with JIT (Just-in-Time) for leaner control. - Real-Time Visibility
Integrate IoT sensors, WMS systems, and data lakes to ensure decision-makers get immediate insights into drop signals and capacity shifts. - Decentralized Warehousing
Enable multiple regional fulfillment points. This reduces load on central hubs and allows selective downscaling based on local demand. - Scenario Testing
Run monthly simulations for various disruption scenarios to identify weak links. Use these simulations to update contingency plans.
At Calcviva, our Adaptability Optimization Suite includes performance heatmaps, supplier ranking systems, and inventory-response algorithms designed to help you systematically improve adaptability scores across supply chain nodes.
Case Study Example
Let’s consider a mid-size electronics manufacturer using Calcviva’s adaptability system. The company faced a significant drop in smartphone demand during a recessionary quarter. Using the Calcviva dashboard, they followed these steps:
- Baseline Output: 10,000 units/week
- Stress Scenario: 40% market demand drop forecasted
- Reduction Target: 6,000 units/week
- Supplier Response Window: 8 days
- Time to Adapt: 14 days
Initial Downside Adaptability:
(4,000 / 10,000) × 100 = 40%
However, adaptation lead time of 14 days was considered too slow. Calcviva tools identified that the delay came from rigid procurement contracts and inflexible shift planning. The company:
- Implemented flexible vendor agreements
- Introduced dynamic labor scheduling
- Added trigger points for early demand detection
Improved Downside Adaptability after 1 month:
- Adaptation Time reduced to 7 days
- Reduction Capability improved to 5,000 units
- New Adaptability: (5,000 / 10,000) × 100 = 50%
This 10% improvement resulted in 12% lower operational costs during the downturn and helped avoid $1.2 million in write-down losses. Calcviva continues to help the business track performance and adjust policies quarterly.
Common Challenges
Despite its importance, many organizations face barriers when trying to measure or improve downside adaptability:
- Data Silos: Poor data sharing between procurement, production, and logistics
- Rigid Supplier Agreements: Inability to modify orders without penalty
- Limited Scenario Planning: Few companies run predictive stress simulations
- Manual Processes: Inability to act on real-time changes due to human bottlenecks
- Overreliance on Forecasting: Assuming accuracy in demand forecasts instead of planning flexibility
Calcviva helps companies overcome these problems through automation, integrated data sources, vendor coordination tools, and continuous adaptability scoring.
Downside vs. Upside Adaptability
While downside adaptability focuses on reducing operations efficiently, upside adaptability is about increasing capacity quickly during demand spikes. Both are part of an agile supply chain strategy.
Feature | Downside Adaptability | Upside Adaptability |
Goal | Reduce output without penalty | Increase output quickly |
Triggers | Demand drops, supply constraints | Demand surges, promotions, new markets |
Measurement Unit | % output reduction capability | % output expansion capability |
Risk Focus | Cost overrun, inventory overflow | Lost sales, service disruption |
SCOR Metric | DSAD | USA (Upside Adaptability) |
At Calcviva, we offer tools to measure both metrics in the same dashboard, providing a complete adaptability profile for planning.
Benchmarks and Industry Standards
The SCOR model and APICS provide adaptability benchmarks across industries. Based on recent data:
Industry | Average Downside Adaptability (%) | Best-in-Class Time to Adapt (Days) |
Electronics | 35–45% | 7–10 days |
Automotive | 30–40% | 10–14 days |
Consumer Goods | 25–35% | 6–9 days |
Pharmaceuticals | 15–25% | 12–18 days |
Businesses should aim to benchmark their adaptability against industry peers using tools like Calcviva, which provides real-time comparison dashboards and sector-specific optimization templates.
Frequently Asked Questions (FAQs)
What is a good downside adaptability percentage?
Over 40% is considered strong in most industries. It means your supply chain can reduce output by 40% without major penalties.
How often should adaptability be measured?
Every quarter or after major supply chain changes. Scenario simulations should be updated monthly.
Can small businesses track adaptability?
Yes, with tools like Calcviva, small teams can input production and inventory data to compute adaptability without ERP systems.
Does adaptability affect supply chain resilience?
Yes. High adaptability increases resilience by allowing quick, strategic responses during disruptions.
Suggestions on Calculating and Improving Supply Chain Downside Adaptability
Downside adaptability is an essential KPI in modern supply chain management. It provides insight into how quickly and efficiently your operations can scale down in response to uncertainty. At CalcViva, we provide the tools, simulations, and data integrations you need to calculate, monitor, and improve this metric. From formula-based calculations to SCOR-aligned benchmarks, this guide offers everything you need to understand how to calculate supply chain downside adaptability and act on the results.